The Future of Calibration: Leveraging IoT and Cloud Platforms for Real-Time Quality Assurance
- shaheer667
- Jun 10
- 3 min read
For Qatar industries, digital transformation is imperative, and the Gulf region is embracing IoT, cloud, and analytics. Calibration, the practice of keeping instruments accurate is evolving too: it’s no longer a periodic, paperwork task but an ongoing, data-driven process. After all, raw sensor data means little if its accuracy isn’t known; experts caution that “if the uncertainty and quality of the data is not known, the data might as well be useless”. Calibration is now essential to unlocking predictive, Industry 4.0 capabilities.
Calibration in the Age of IoT and Cloud
Today’s connected sensors and cloud platforms make calibration continuous and collaborative. Instrument outputs can stream into centralized IIoT systems so that calibration logs are no longer siloed. In the cloud, companies can apply analytics and machine learning to vast calibration data sets, unlocking insights and scalability. For example, an automated system might spot that a pressure gauge is drifting out of tolerance and alert the team immediately, rather than waiting for the next manual check. Integrating calibration data with enterprise IT systems also improves oversight: one analysis notes that keeping OT data isolated means missing out on “compliance benefits” and centralized monitoring.
Benefits of Real-Time, Data-Driven Calibration
● Faster Compliance Reporting: Cloud-based calibration platforms enable instant report generation. Users can produce standardized calibration reports and certificates with one click, complete with electronic signatures and watermarks. These can be distributed across all sites automatically, drastically reducing manual paperwork and speeding up regulatory audits.
● Centralized Data Management: All instruments’ calibration histories reside in a secure cloud repository. Technicians and managers can retrieve any equipment’s full calibration record from anywhere, eliminating the need for disconnected spreadsheets or filing cabinets. This single source of truth improves collaboration and ensures every audit detail is captured.
● Improved Traceability: Digital systems automatically log each calibration event and track an instrument’s status over time. With this visibility, patterns and deviations become apparent. For instance, if a sensor’s output is gradually drifting, analytics can flag it early so technicians can intervene. The full audit trail is at hand, strengthening quality assurance and meeting compliance requirements.
● Reduced Human Error: Automating calibration steps cuts out manual data-entry mistakes. Machine-readable certificates and electronic data capture mean technicians no longer transpose values by hand. These standardized digital processes improve accuracy and consistency, and reduce the risk of lost or misfiled records.
● Predictive Calibration: Data-driven insights can trigger calibrations based on actual usage and performance trends. Instead of fixed schedules, instruments are serviced just-in-time. In fact, cloud platforms can optimize calibration intervals, for example, increasing frequency when safety demands it, to prevent failures before they occur. This predictive approach improves safety and can even lower lifecycle costs by avoiding unplanned downtime.
Relevance for Qatar’s Key Industries
These digital calibration advances are especially impactful in Qatar’s core sectors. Oil & gas and energy facilities deploy thousands of pressure gauges, flow meters and analyzers under strict regulatory regimes. By connecting these devices to a cloud system, companies can automatically verify they remain in tolerance and receive instant alerts if any instrument drifts, keeping operations safe and compliant. In manufacturing and construction, real-time calibration data minimizes downtime and helps maintain quality standards on complex projects. For all these industries, centralized calibration data also simplifies audits, boosting operational confidence just as Qatar pushes forward on its Smart Qatar and industrial growth agendas.
Vertex Calibration: A Forward-Thinking Partner
As a thought leader in the region, Vertex Calibration is guiding clients every step of the way. We combine decades of metrology experience with forward-looking expertise in IoT and cloud integration. Rather than push any specific product, we advise on best practices for data governance, connected sensors and digital workflows. Our role is to ensure each client’s calibration strategy remains robust, compliant and future-ready. By working closely with engineering and operations teams, Vertex helps make calibration seamless and smart, freeing our partners to focus on core challenges with confidence.
In conclusion, the future of quality assurance depends on connected calibration. Accurate measurements will be built into live data streams and analytics, not buried in paperwork. By embracing IoT and cloud platforms now, companies in Qatar can accelerate compliance processes, improve traceability, and reduce errors, turning calibration into a competitive advantage. The question for every engineering leader is: are you ready to transform calibration from a periodic chore into a real-time strategic asset?
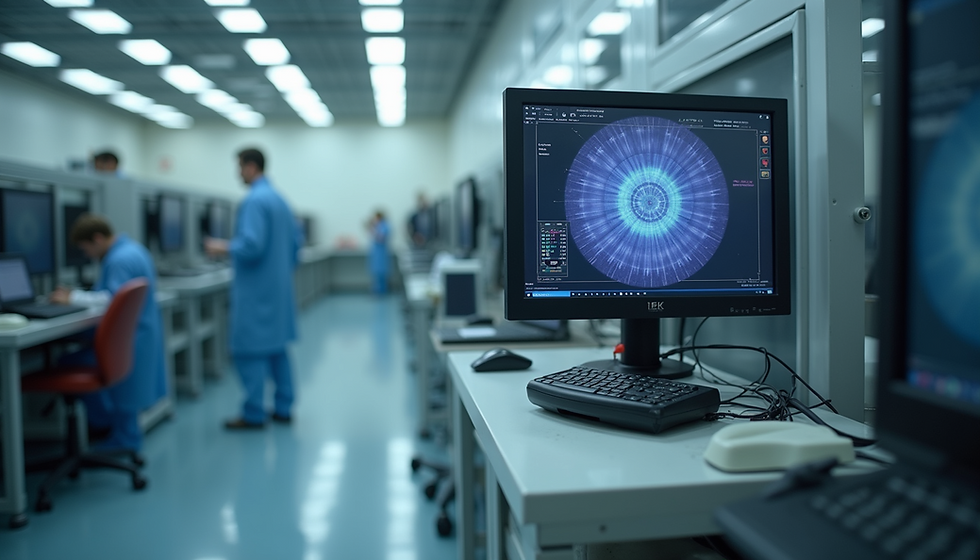
コメント